Our Story
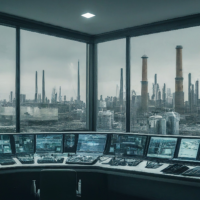
NetCEMS has the unique design on the CEMS controls via 100% Ethernet-based network. It is far more superior to the traditional PLC controls, which is always in the single-point-of-failure mode. Every control HMI is using TCP/IP protocol to communicate with I/O devices. No ladder logic programming is needed. All signals are terminated at the source to the Ethernet-based distributed I/O modules, which communicate to the primary CEMS controller. When the primary controller is down, the secondary controller, which runs on the same network, will take over the task. If it fails, the third one will start to work.
With the progress in the software technology, the CEMS control goes “virtual”. When we run CEMS control logics on the different server hardware, VM (virtual machine) controls CEMS via network at the fraction of the cost on hardware infrastructure, yet at the highest fault-tolerant level.
The redundant CEMS controls give our clients peace of mind of avoiding PLC communication errors, program halts and lock-ups. With triple-redundancy via either hardware controllers or VM software controllers, the CEMS availability is virtually 100%.